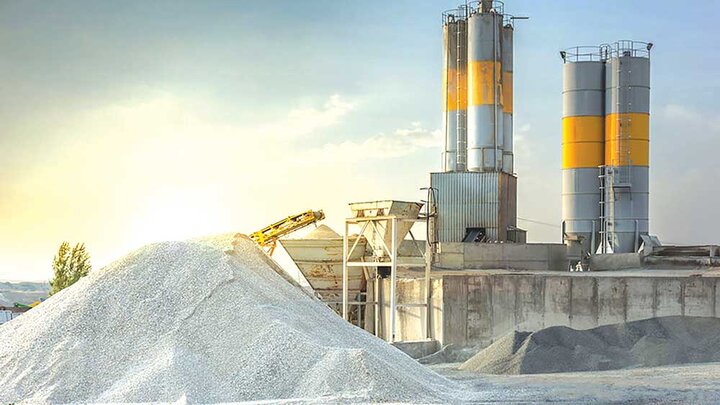
بیش از ۱۸۰ سال از شروع مصرف انبوه سیمان پُرتلند (Portland Cement) میگذرد و اکنون این فرآورده به یکی از مهمترین مصالح ساختمانی تبدیل شدهاست. بررسی میزان تولید و مصرف جهانی سیمان پرتلند به این مفهوم است که سیمان به عنوان یک کالای صنعتی، دارای بالاترین رقم تولید در میان تمام کالاهای صنعتی است.
کلمه سیمان در لغت به معنای چسب بوده و منظور از سیمان در مصالح ساختمانی، چسبی است که در اثر ترکیب با آب، قادر به چسباندن ذرات شن و ماسه (سنگدانه) است و پس از سفت شدن نیز در آب حل نمیشود. این نوع سیمان، سیمان هیدرولیک خوانده شده و اساساً از اکسید کلسیم تشکیل میشود. این اکسید با اکسیدهای آلومینیوم، سیلیسیم و آهن ترکیب شده و ترکیبات معدنی یا فازهایی با خاصیت سیمانی را ایجاد میکنند.
اگرچه بشر از هزاران سال پیش با مصالحی که خاصیت هیدرولیکی دارند و پس از سخت شدن، در آب حل نمیشوند، آشنایی پیدا کردهبود، اما از حدود ۲۳۰ سال پیش بود که بررسیهای علمی و سیستماتیک بر روی این گونه ملات و عوامل اصلی سیمانی بودن آنها شروع شد.
در ابتدای کار از کورههایی مشابه با کورههای آهکپزی برای تولید سیمان استفاده میشد و به دلیل استقبال زیاد از آن، در اواخر قرن نوزدهم، کورههای دوّار ابداع شد و هماکنون تکنولوژی به حدی است که با حداقل انرژی ممکن مصرفی و نیروی انسانی، کورههایی با ظرفیت ۱۰۰۰۰ تُن در روز عرضه میشود.
مواد اصلی به منظور تولید سیمان عبارتند از : سنگ آهک و خاک رس (سلیس و آلومین) که در طبیعت به وفور یافت میشوند ولی به شکلی نیستند که بتوان از آنها به طور مستقیم در تولید سیمان استفاده کرد.
سیمان شامل چه ترکیباتی است؟
آهک زنده یا اکسید کلسیم (CaO)
آهک زنده یا اکسید کلسیم از اصلیترین مواد در ساخت سیمان است. اکسید کلسیم از پختن سنگ آهک یا کربنات کلسیم در حرارت حدود هزار درجه سانتیگراد به دست میآید. این فرآیند به طور جداگانه انجام نشده و در فرآیند تولید سیمان و در موقع حرارت دادن پودر مخلوط آهک و خاک رس، ابتدا ذرات آهک (کربنات کلسیم) در حرارت حدود ۱۰۰۰ درجه سانتیگراد پخته شده و تبدیل به اکسید کلسیم و یا آهک زنده میشود. در این گرما، آب شیمیایی خاک رس نیز از آن جدا میشود. در درجه حرارت بیشتر از ۱۰۰۰ درجه سانتیگراد، اکسید کلسیم (آهک زنده) با اکسیدهای سیلیسیم، آلومینیوم و آهن ترکیب شده و فازهای سیمان تشکیل میشوند.
سیلیس (SiO2)
این ماده که در اغلب سنگهای طبیعی یافت میشود، یکی از مواد اصلی در ساخت سیمان پرتلند است. وقتی سیلیس حرارت داده میشود، در ساختمان کریستالی آن، تغییراتی به وجود میآید. در کوره سیمانپزی در حدود ۱۴۰۰ درجه سانتیگراد سیلیس با آهک ترکیب شده و سیلیکات تشکیل میشود. خاک رس معمولی دارای مقادیر زیادی سیلیس است. میزان سیلیس مورد نیاز، ۱۷ تا ۲۶ درصد وزن سیمان است و چنانچه نتوان این مقادیر را با استفاده از خاک رس معمولی فراهم کرد، میتوان آن را با استفاده از سایر منابع، تأمین کرد.
آلومینا (Al2O3)
آلومینا یا اکسید آلومینیوم خالص، به مقدار زیادی در خاک رس وجود دارد. آلومینا در سیمانپزی اثر کمکذوب و در هنگام پخت سیمان، درجه حرارت پخت مواد خام را کاهش میدهد. از نظر شیمی سیمان، در اثر حرارت داخل کوره دوّار، با آهک ترکیب شده و تشکیل سه کلسیم آلومینات را میدهد. وجود این اکسید مرکب در داخل سیمان تولیدی، باعث میشود سیمان زودتر بگیرد و در هنگام ترکیب سیمان با آب، حرارت بیشتری ایجاد شود. ملات سیمانی که اکسید سه کلسیم آلومینات کمتر از ۵ درصد باشد، در برابر آب دریا و سایر آبهای سولفاتدار مقاوم است و تخریب نمیشود.
اکسید آهن (Fe2O3)
اکسید فریک نیز همانند آلومینا در سیمانپزی نقش کمکذوب را دارد و باعث کاهش درجه حرارت پخت مواد خام در داخل کوره میشود. این اکسید در داخل کوره و در هنگام پخت، به همراه آلومینا با آهک ترکیب شده و تشکیل اکسید مرکب چهار کلسیم آلومینوفریت را میدهد. اکسید آهن، اصلیترین جزء تشکیلدهنده اغلب سنگ آهنها است؛ از این رو، اکسید فریک، کم و بیش در اغلب کانیها خاک رس، و در اغلب مواد اولیهی ساخت سیمان وجود دارد. در سیمان پرتلند تولیدی نیز اکسید مرکب آن به وجود میآید که رنگ سیمان را تیره میکند. لازم به ذکر است که سیمان سفید فاقد اکسید آهن است.
برچسب ها: ربات آربیتراژ و ربات آربیتراژ قطعا سودده و ثبت نام ربات آربیتراژ و سفارش ساخت ربات فارکس و ساخت ربات معامله گر بورس و ساخت ربات معاملاتی و طراحی ربات تریدر و ربات فارکس رایگان و برنامه نویسی ربات فارکس و آموزش ساخت اکسپرت فارکس و ساخت ربات معامله گر با پایتون و دانلود ربات معامله گر فارکس و خرید ربات تریدر فارکس و ربات فارکس خودکار و ربات معامله گر بورس رایگان و آموزش ساخت ربات معامله گر فارکس و دانلود ربات معامله گر بورس ایران و ربات معامله گر آلپاری و ربات فارکس برای اندروید و ربات سود ده فارکس و ربات سود ده بورس ایران و اکسپرت سود ده فارکس و اکسپرت سود ده بورس ایران
اکسید منیزیم (MgO)
این اکسید در فرآیند پخت، نقش کمکذوب را ایفا میکند و نباید از مقدا معینی (۵ درصد) بیشتر باشد، زیرا با سایرترکیبات سیمان ترکیب و وارد فازهای سیمانی نمیشود و آزاد در سیمان باقی میماند. نظر به اینکه MgO پس از گرفتن ملات سیمان خیلی به کندی با آب ترکیب شده و منجر به انبساط حجمی میشود. در نتیجه، تَرَکهای موئی در ملات سیمان و بتن ایجاد میشود که در طول زمان باعث تخریب آنها میشود. بنابراین، اکسید منیزیم نباید در سیمان بیشتر از ٪۵ وزنی آن باشد.
◊ این مطلب را حتماً بخوانید: آموزش تحلیل بنیادی
قلیائیها
سدیم و پتاسیم در فرآیند تولید سیمان نقش روانسازی داشته و مقدارشان نباید بیشتر از ۱ درصد وزن آن شود. مقدار کلر در کلیه سیمانها به جهت نقش تخریبی آن در بتن، بایستی کمتر از ۰/۱ درصد وزنی آنها باشد. مقدار قابل قبول انیدرید سولفوریک درسیمانهای پرتلند، روبار و پوزولانی بستگی به میزان سطح مخصوص (بلین) آنها دارد. اگر سطح مخصوص آنها بین ۲۰۰۰ الی ۴۰۰۰ سانتیمتر مربع بر گرم باشد، ۳/۵ درصد وزنیِ سیمان است و اگر چنانچه سطح ویژه سیمان بیش از ۴۰۰۰ سانتیمتر مربع شود، ۴ درصد وزنیِ سیمان است. لازم به ذکر است که سنگ آهن به عنوان کمکذوب به مواد اولیه اضافه میشود.
فرآیند تولید سیمان شامل چند مرحله است؟
مرحله اول – مواد اولیه
مواد قلیایی
- آهن
- آلومینیوم
- سیلیسیم
مواد آهکی
- کلسیم
بر اساس تکنولوژی موجود در سایت تولید سیمان، ترکیبی از این مواد اولیه، به واحد تولید وارد میشود.
مرحله دوم – آسیاب مواد خام
در این مرحله، مواد اولیه ورودی به واحد تولیدی، در آسیاب ابتدایی قرار گرفته و یا با هم ترکیب میشوند.
مرحله سوم – ذخیرهسازی مواد خام
پس از آسیاب مواد خام و ترکیب آنها با یکدیگر، این مواد، در واحد ذخیرهسازی مواد خام قرارمیگیرند تا به مرحله بعد منتقل شود.
مرحله چهار – تولید کلینکر
در این مرحله، مواد خام آسیابشده در کوره حرارت داده میشوند (در دمای ۱۵۰۰ درجه) (حرارتدهی ابتدایی) و پس از حرارت دیدن، به کوره دوّار منتقل میشوند. خروجی واحد کوره حرارتی دوّار، کلینکر یا ماده ابتدایی تولید سیمان است.
مرحله پنج – تولید سیمان
کلینکری که در مرحله قبل تولید و در سیلوی کلینکر ذخیره شد، به آسیاب سیمان منتقل شده و به کلینکر گچ و ترکیبات دیگر اضافه میشود. خروجی این واحد، سیمان نهایی است.
مرحله شش (نهایی) – ذخیرهسازی و ارسال
سیمان تولیدشده، حالا به سیلوهای ذخیرهسازی سیمان منتقل شده و در این واحد ذخیره و نگهداری میشود.
دیدگاهها (0)